The MGA With An Attitude
FUEL PUMP BRACKET, Welded Frame - FR-123
The MGA frame weldment fuel pump bracket (in process). Photos and sketches compliment of Peter Ryle. Working on this in late January 2022.
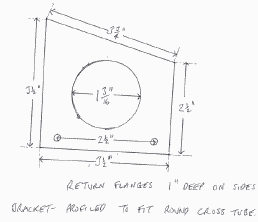
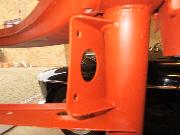
I made a preliminary CAD drawing, and sent it to Peter with a few questions. Second pass sketch at right makes the tube horizontal angle 25 degrees, and 10 degrees from the transverse plain, 2" diameter for the tube, and 1.47" diameter for the large hole. I will take a second pass at the drawing later.
Meanwhile another friend jumped the gun and made a bracket using first pass information with a bit of fettling to make it fit. See pictures below. Close, but no cigar. We can do better. Stand by.
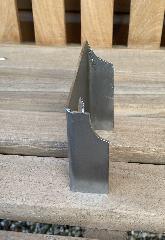
Okay, another half day of layout work to do it over with 15-degree incline and 5-degree forward angle on the 2-inch diameter tube, and we get this. Reason for the exact CAD drawing is to get the ellipse interface correct. After the final layout in the flat with proper bend allowance, the low-angle ellipse is changed to the nearest matching simple radius (within 0.010-inch) to simplify layout and cutting (or punching) on sheet metal flat stock.
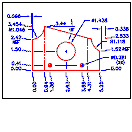
And finally we have a template. Click for PDF document, and print it on A-size (8-1/2" x 11") paper. It should print with 1/2-inch margins, 10" x 7.5" border line for exact full scale template.
Suggest taping it down on the sheet metal stock (14-gauge, 0.075" thick), center punch the centers of the circles and all corners. Scribe cutting lines between the punch marks and on the two open radius, cut on the lines and de-burr.
Bend down 90 degrees on the phantom lines. Designed to have 0.040" inside radius, or half the material thickness (or as near zero radius as you like). Do be sure to bend it in the correct direction. Bending will stretch the material length and distort the edges slightly. You might want to touch up the top corners after forming where it will mate with the round frame tube before welding. When installed it should look like first picture at top of page, straight up vertical.
|