The MGA With An Attitude
MGAguru.com |
The Electric MGA, from UTA - ET-301J |
MGAguru.com |
Conversion of an MGA to Electric Power by engineering students at UTA


1957 MGA Electric Conversion
Team Lead:
Powertrain:
Power System:
Chassis:
Schedule/Budget:
|
Steve Gillespie
Rich Bergs
Jay Krueger
Hank Danford
Chris Pickering
|
|
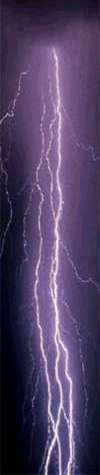
|


Presentation Overview
- Project Overview
- Motor System Comparisons
- Battery Comparisons
- Designed Adaption Components
- Schedule
- Budget
- Conclusion
|
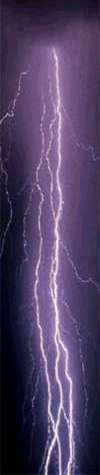
|


Required Performance
- Able to reach and maintain 40-50 mph
- A range of 20 miles per charge
- Able to climb grades
- Accelerate in a reasonable amount of time
|
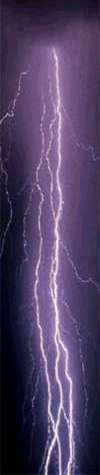
|


Modeling of Vehicle
- Results of Model
-Required power output at speed
-RPM range required of system
-Effects of added weight to performance
|
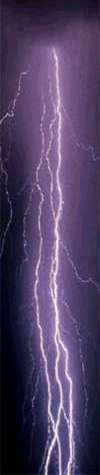
|


Systems Considered
- Brushed DC
-System used for comparison: FB1-4001
- Brushless DC
-System used for comparison: CaliberEV 32
- AC
-System used for comparison: AC42A
|
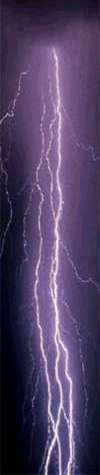
|


Brushed DC System
- Pros
-Pricing
-Availability
-Lowest Voltage
|
- Cons
-Efficiency
-Maintenance
-Lowest Voltage
|
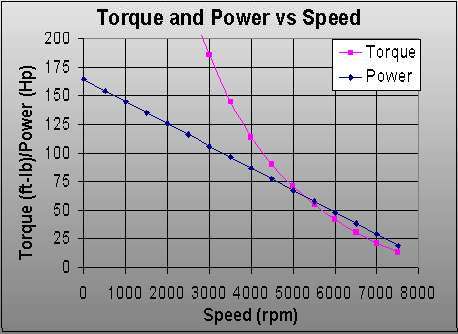
|
|
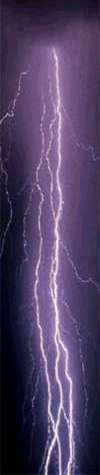
|


Brushless DC System
- Pros
-Regenerative Braking
-No Major Maintenance
-Low Voltage
|
- Cons
-Availability
-Cost
-Low Power Output
-Low Voltage
|
|
|
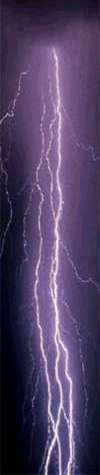
|


AC System
- Pros
-Regenerative Braking
-No Major Maintenance
-High Voltage
-High Power Output
|
- Cons
-Availability
-Cost
-High Voltage
|
|
|
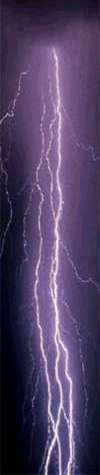
|



Choice of System
- Brushed DC
-Top Speed ? 90 mph
-0 to 60 = 10 sec.*
- Brushless DC
-Top Speed ? 80 mph
-0 to 60 = 17 sec.
- AC
-Top Speed ? 102 mph
-0 to 60 = 15 sec.
|
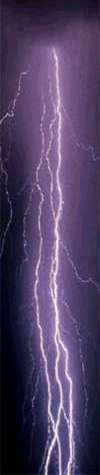
|


Battery
Genesis 42EP
Hawker Energy Products, Inc.
- Size
LxWxH 7.78 x 6.53x6.72
- Weight
33 pounds
- Power
394 Wh
- Cost
$141.00 Delivered.
|
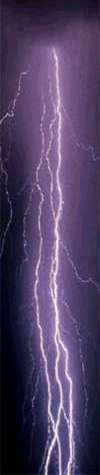
|


Front Battery Box
- Material
AISI 1040 CR 16 Gage (1/16”)
- Size
LxWxH 21x24x9
- Box Weight
24 pounds
- Assembly Weight
340 pounds
|
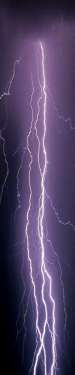
|


Behind Seat Battery Box
- Material
AISI 1040 CR 16 Gage(1/16”)
- Size
LxWxH 10x14x9
- Box Weight
10 pounds
- Assembly Weight
80 pounds
|
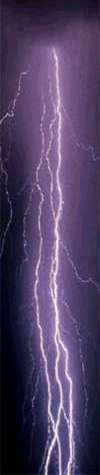
|


Rear Battery Box
- Material
AISI 1040 CR 16 Gage (1/16”)
- Size
LxWxH 21x33x9
- Box Weight
31 pounds
- Assembly Weight
480 pounds
|
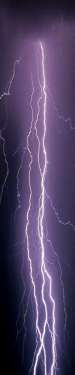
|


Front Battery Box Analysis
- Applied Force
3G =1050 lb
- Deflection (shown)
Less than 0.001”
- Stress
16.5 kpsi
- Conclusion
Stress is below yield strength of material (60 kpsi) by factor of 3.6
|
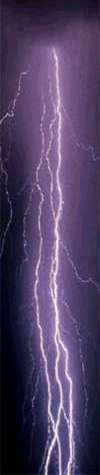
|


Rear Battery Box Analysis
- Applied Force
3G =1050 lb
- Deflection (shown)
Less than 0.006”
- Stress
18.7 kpsi
- Conclusion
Stress is below yield strength of material (60 kpsi) by factor of 3.2
|
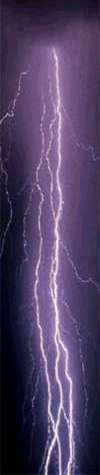
|


Battery Summary
- 25 Batteries connected in series
- 4 Battery boxes
- 900 lb of added weight to car
- 76 mile range at 45 mph
|
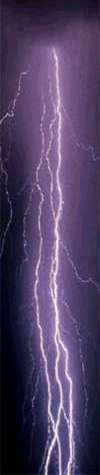
|


Chassis Considerations
- Frame is welded, steel box section
- Cross-braced and has integral suspension mounts
- Very strong; designed with endurance capacity for racing
|
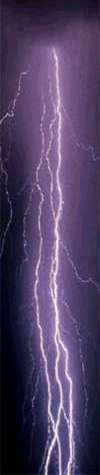
|


Brakes
- Four wheel drum brakes
(10 inch)
- Convert front to disk brakes
(maybe rear also)
- MGB parts to upgrade or
use after market kits
|
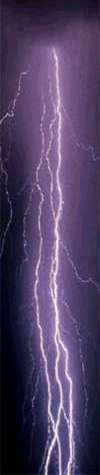
|


Shocks/Springs/Other
- Rebuild or upgrade stock lever shocks (heavy duty shock valves)
- Upgrade front coil springs and rear leaf springs
- Add front sway bar (maybe rear also)
- Polyurethane bushings where applicable
|
- Weight Distribution
-Original Curb Weight 1862 lbf
= Front 52%
= Rear 48%
-Estimated Final Curb Weight 2450 lbf
= Front 45%
= Rear 55%
|
|
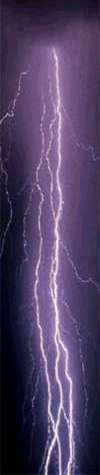
|


Motor Controller Mounts
Mounts to existing brackets in engine compartment
AISI 1030 12 gage steel
|
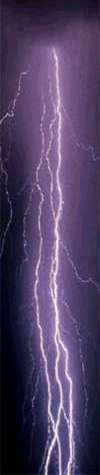
|





Schedule
- Approximately 1 week behind schedule
-Air Control Design
-Regenerative Braking Design
* Manual from Motor System Needed
-Motor Mount Design - 25%
* Final Specifications on Motor Needed
-Transmission Design - 80%
-Controller Mounting Design - 80%
|
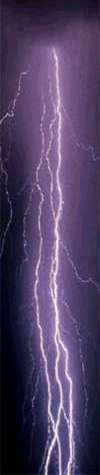
|


Budget
- Over Budget
- Components
* Motor $291
* Controller $250
* Batteries $825
|
- Under Budget
- Components
* Throttle Pot Box $170
* Miscellaneous $2,548
* Materials $1,352
- Labor
* Engineering Hours $8,981
|
- Bottom Line
- Budgeted-Spent
* $74,223 - $63,890 = $10,333
|
|
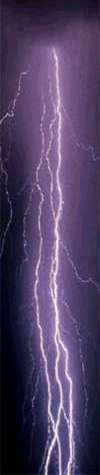
|


Conclusion
Purpose
Motor/Controller
- Solectria AC42A/UMOC440TF
Battery
- Hawker Genesis G42EP
Adaption Components
- Component Design and Analysis as Complete as Possible
Chassis
- Chassis Modification Not Needed
Schedule
- 1 Week Behind
Budget
- Under By $10,333
|
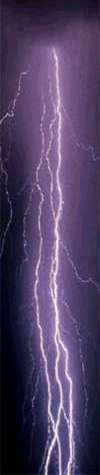
|
|
|
|